Leading the Way: Your Premier Plastic Injection Molding Supplier
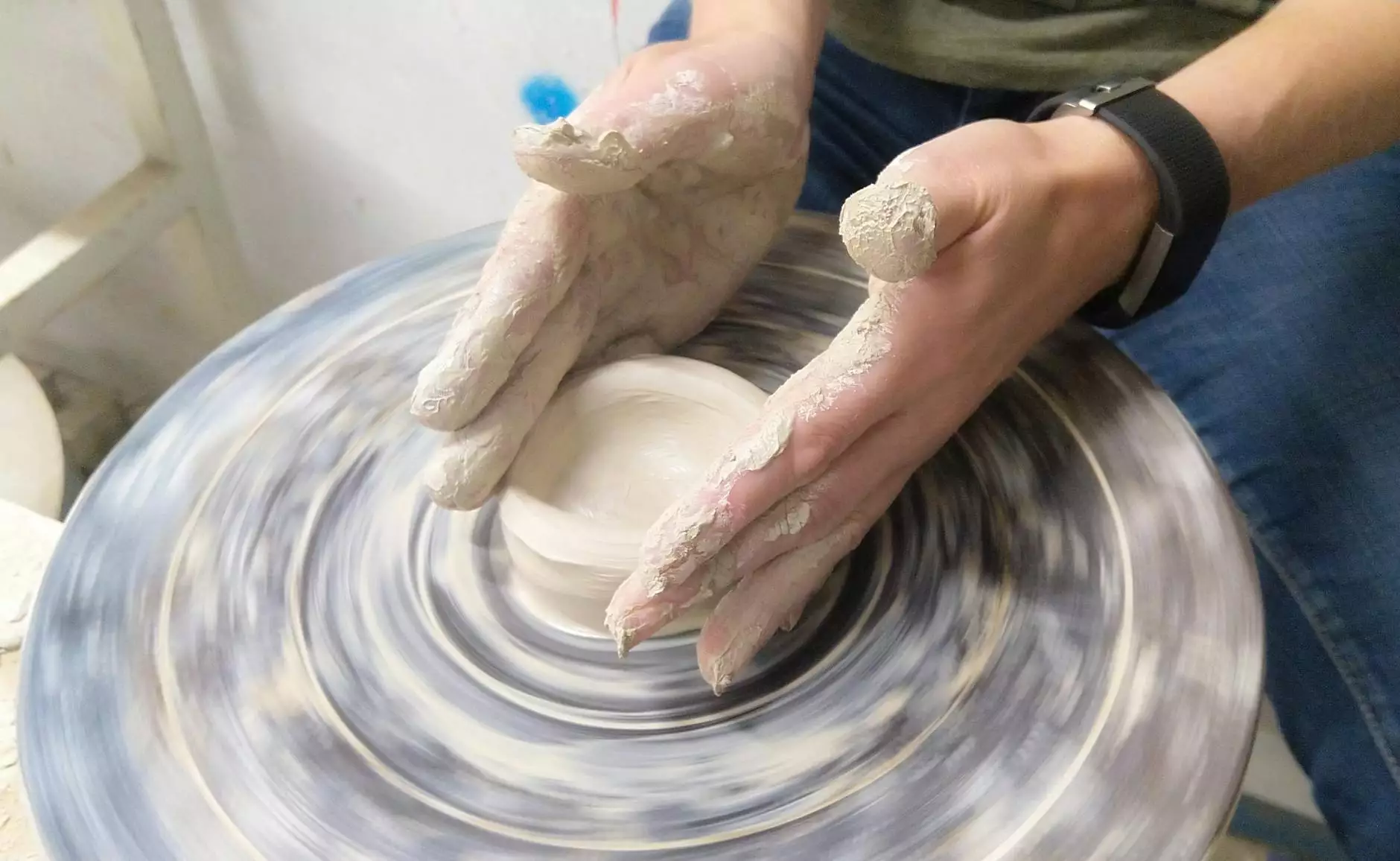
The world of manufacturing is evolving rapidly, and with it comes the need for efficient, cost-effective solutions that meet the increasing demands of various industries. As a plastic injection molding supplier, we at Deep Mould are poised to meet these demands through our advanced technology and processes. In this article, we will delve deep into the intricacies of plastic injection molding and illustrate why partnering with a reputable supplier is pivotal for your business success.
Understanding Plastic Injection Molding
Plastic injection molding is a complex process that involves producing parts by injecting molten plastic into a mold. This process is favored across several industries due to its ability to create precise, consistent, and high-quality parts. The following are key stages in the plastic injection molding process:
- Mold Design: This is where the first step occurs. A mold is designed to create the desired shape of the component.
- Material Selection: Choosing the right material is crucial. Various types of plastics can be used, ranging from thermoplastics to thermosetting plastics.
- Injection: The molten plastic is injected into the mold under high pressure, allowing it to fill every cavity.
- Cooling: Once injected, the material must cool and solidify before being ejected from the mold.
- Ejection: The final step involves ejecting the cooled part from the mold, ready for use or further processing.
The Importance of Choosing the Right Supplier
Choosing the right plastic injection molding supplier is critical for your business's efficiency and success. A reputable supplier brings numerous advantages to the table, including:
- Expertise and Experience: A seasoned supplier has a deep understanding of the industry and can provide valuable insights.
- Quality Control: Reliable suppliers adhere to stringent quality standards, ensuring that every part meets your specifications.
- Cost Efficiency: By optimizing manufacturing processes, a good supplier can help reduce overall costs.
- Innovation: A top-tier supplier invests in the latest technologies, ensuring that you receive the best products available.
- Customer Service: Having a dedicated support team means you can resolve issues quickly and maintain production schedules.
Benefits of Plastic Injection Molding
The benefits of using plastic injection molding are far-reaching, which include but are not limited to:
1. High Production Rates
Plastic injection molding can produce large volumes of parts rapidly, making it ideal for high-demand products. The process is automated, significantly increasing output while minimizing labor costs.
2. Design Flexibility
One of the most significant advantages of plastic injection molding is the ability to produce complex shapes and designs. The precision of the molds allows for intricate details and nuanced features that would be impossible with other manufacturing methods.
3. Material Variety
We provide a wide range of materials, including thermoplastics, which can be molded and remolded, and thermosetting plastics, which can withstand higher temperatures. This versatility allows businesses to select the material that best fits their product requirements.
4. Waste Reduction
Injection molding produces minimal waste compared to other manufacturing methods. Excess material can often be recycled, leading to a more sustainable production process.
5. Cost-Effectiveness
While the initial costs of designing a mold can be high, the ability to mass-produce parts means that the overall cost per unit is significantly lower. This is particularly beneficial for businesses looking to scale production.
Applications of Plastic Injection Molding
The applications of plastic injection molding are vast, serving various sectors including:
1. Automotive Industry
Components such as dashboard panels, bumpers, and other interior and exterior parts are commonly manufactured through injection molding, providing durability and aesthetics.
2. Consumer Products
From kitchenware to toys, many everyday items are produced using plastic injection molding, as it allows for attractive designs and high durability at a low cost.
3. Electronics
Injection molding is instrumental in creating casings and components for electronic devices, ensuring they are lightweight and robust.
4. Medical Devices
As precision and reliability are critical in healthcare, plastic injection molding is extensively used to produce devices and components like syringes, surgical instruments, and housings for electronic devices.
5. Industrial Applications
Parts used in manufacturing machinery, equipment, and tools often rely on the efficiency and accuracy of injection molding processes.
Quality Assurance: The Deep Mould Commitment
At Deep Mould, we understand that quality is paramount in production. Our commitment to quality assurance includes:
- Regular Inspections: Every production run is subject to meticulous inspections to ensure compliance with standards.
- Testing Protocols: We implement rigorous testing methods to assess the performance and safety of each part.
- Process Optimization: Continuous improvement processes are in place to enhance manufacturing efficiency and product quality.
The Future of Plastic Injection Molding
As technology continues to advance, so does the field of plastic injection molding. Future trends to keep an eye on include:
1. Automation and Smart Manufacturing
With the rise of industry 4.0, automated injection molding systems and the integration of IoT technologies are set to revolutionize the process, enhancing efficiency and precision.
2. Sustainable Practices
There is a growing demand for environmentally-friendly materials and processes. The focus on recyclability and biodegradability in plastic products will shape the future landscape of injection molding.
3. Advanced Materials
Continued research and development in new materials will pave the way for stronger, lighter, and more versatile injection-molded products.
How to Choose the Right Plastic Injection Molding Supplier
When selecting a plastic injection molding supplier, consider the following factors:
- Experience: Look for a supplier with a proven track record and expertise in your industry.
- Capabilities: Ensure the supplier can handle your specific project requirements, including material selection and production volume.
- Reputation: Research customer testimonials and case studies to gauge the supplier's reliability and quality of service.
- Support: A good supplier should offer comprehensive support throughout the production process, including design assistance and post-production services.
Conclusion
In conclusion, collaborating with a high-quality plastic injection molding supplier like Deep Mould can significantly enhance your production capabilities. With our commitment to quality, innovation, and customer satisfaction, we are equipped to meet your manufacturing needs. Contact us today to learn how we can help your business thrive!
If you’re interested in diving deeper into the world of plastic injection molding and how our services can benefit you, feel free to reach out to us for more information.